2007年4月16日SANTACRUZ工場見学
カリフォルニア州サンタクルーズにある工場を見学に行きました。
新たに日本の輸入代理店となったトーラスコーポレーションの中村社長のはからいで、大阪ドルフィンギターの武田さんとともにおじゃましました。
案内してくれたのは、ダン氏で、工場責任者です。
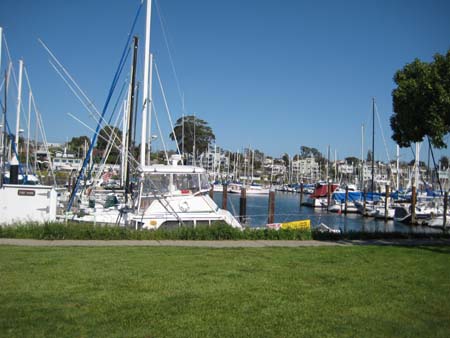 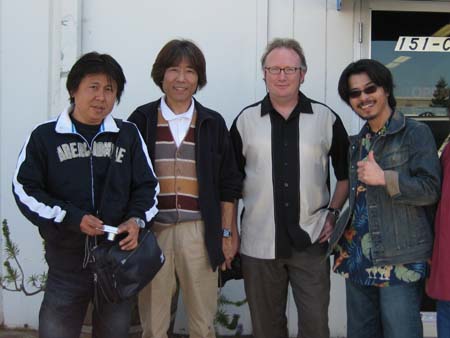
サンタクルーズは美しいリゾートな街で、海は綺麗でヨット、サーフィンとマリンスポーツのメッカでもあります。
写真左はヨットハーバーで、ここからホエールウォッチングにヨットで出かけました。
写真右は工場にて、左から武田さん、中村さん、ダン、私です。
それでは、工場の様子です。
思った以上に広い工場で驚きましたが、作業はほとんどハンドメイドで、職人さんの手による手間のかかった製作手順でした。
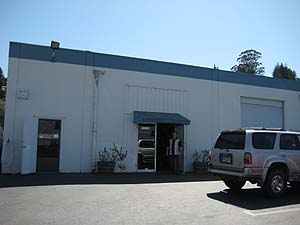 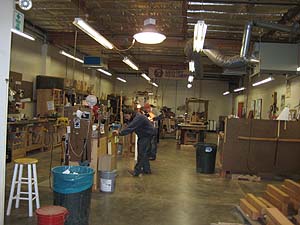 材質の保管は工場内で、生産数量が少ないせいか、工場の材料保管ブースとしては、かなり少ないように思いました。
ハカランダやコアウッドといった希少材も見られました。
 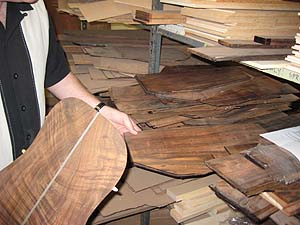 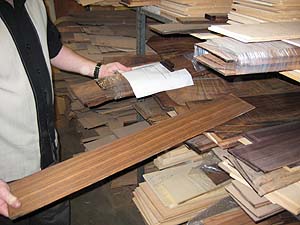
自然乾燥済みの材を、強制乾燥ルームでさらに乾燥させてから製作に入ります。
下左の写真が強制乾燥ルームで、真ん中がセット機械です。
下右は、製品の仕様書で、白いものがレギュラー品、青い紙がカスタムショップ品で、約半分がオーダーメイドのカスタムショップです。
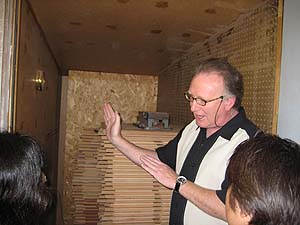 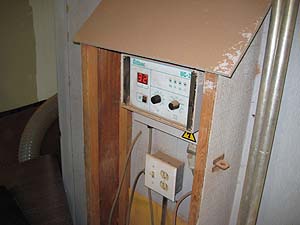 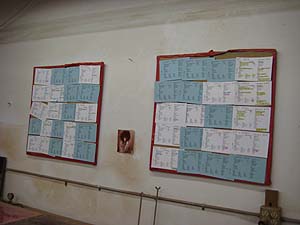
写真左下はコンピューターによる3D設計ソフト、これをマシンで削り出しします。
実際の工程は、職人さんがそれぞれの持ち場で、ひとつひとつを手作業で仕上げていました。
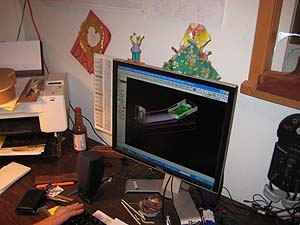 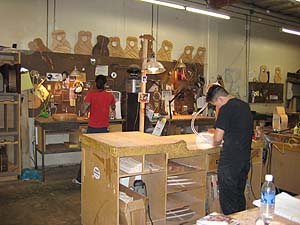 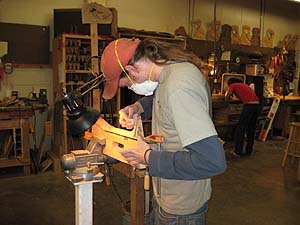
下左のダンが説明しているのは、サイド材の整形型で、一本一本、熱をかけて整形していきます。
トップ材、バック材は一枚一枚を指でたたいて音の響きを確かめながら、厚みを削っているところです。
材質の特性にあわせて、最良の響きを出せるように、一本一本微妙に厚みが違います。
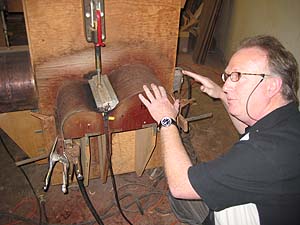 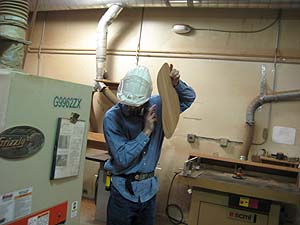 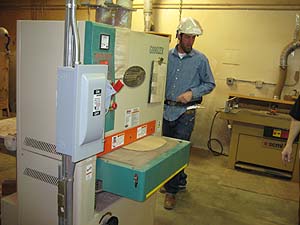
トップ板も厚みを削ったあとにブレイシングを接着し、その後、丹念に指で音を聞きながらノミでブレイシングを削って行きます。
楽器の音を決定付けるこの作業は、熟練した職人が一人で担当しています。
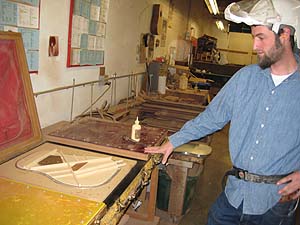 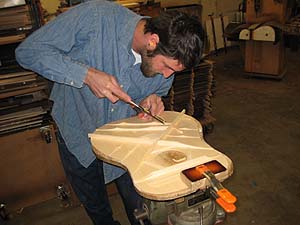 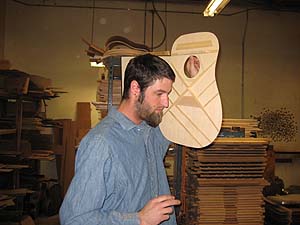
トップ、バックの接着やバインディング作業も、それぞれ、担当の職人の手で丁寧に作業されています。
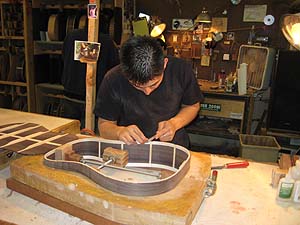 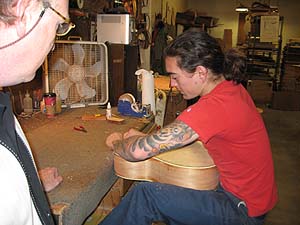 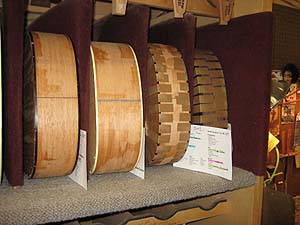
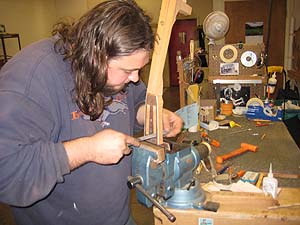 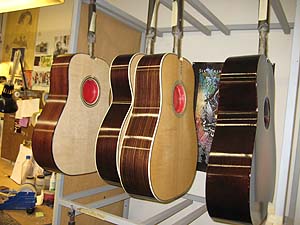 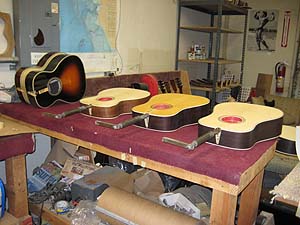
工程では、基本的に一本一本を手作業で製作していますので、作業中の楽器では同じ楽器が並んでいることはありませんでした。
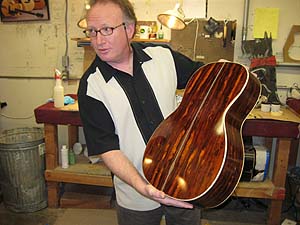 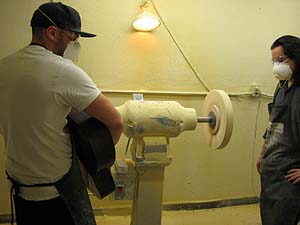 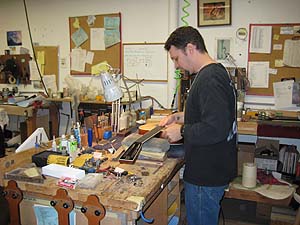
仕上げ、セティングも手間をかけて行われています。
下右の写真は、工場近くの海で、先ほどブレイシングを削っていたジョンが、昼休みにサーフィンをしているところです。
良い環境ですよね。
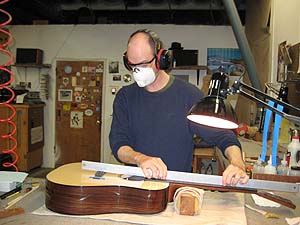 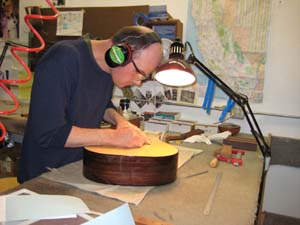 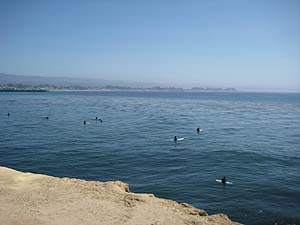
工場見学のあと、サンタクルーズの招待でヨットでホエールウォッチング(鯨)につれて行ってもらいました。
私のカメラでは写っていませんでしたが、イルカがジャンプしたり、一頭だけでしたが鯨も見ることが出来ました。
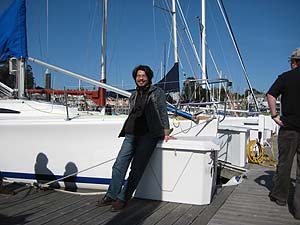 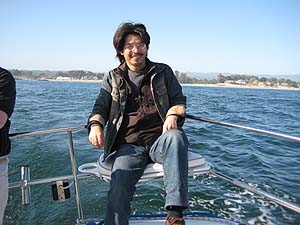
今年から、トーラスさんでサンタクルーズのギターを扱うことになり、当店も販売店としてお取り扱いするため、今回、見学に行かせてもらいました。
サンタクルーズは、日本では輸入代理店が転々として、楽器のクオリティーの割りに評価されていないですが、あらためて工場を見せてもらい、製作現場を見ると、量産楽器には無い魅力を感じました。
楽器を製作する手順が、個人ビルダーと同等の手をかけており、そのうえで工場としてある程度の数を製作して、それなりのコストを実現していることが、楽器の良さにつながっていると思います。
まだ、当店では在庫は少ないですが、カスタムオーダーもあわせて、リクエストがございましたらお気軽にお問い合わせください。
|
|
|
|